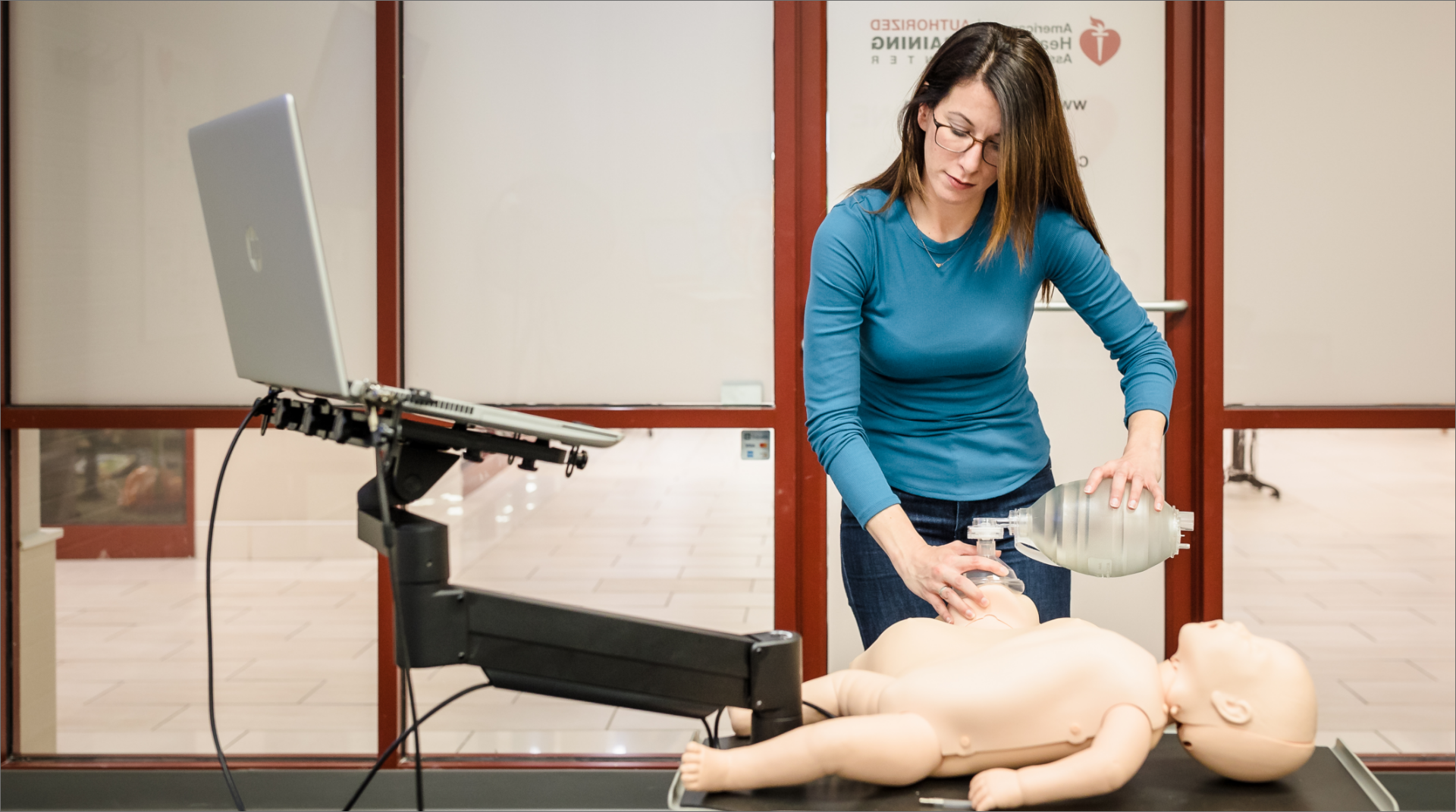
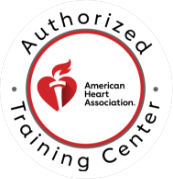
CPR Resource Center
The most comprehensive library of emergency training resources — including videos, articles, downloads, and more.
The most comprehensive library of emergency training resources — including videos, articles, downloads, and more.
As the Health and Safety Manager of your workplace, you’ve finally completed the seemingly endless process of researching, budgeting, purchasing, and installing an Automated External Defibrillator (AED) on the wall of the break room. You’ve arranged for a team of employees to undergo Heartsaver CPR AED training with the American Heart Association. Now it’s time to check this task off your list and move on to the dozens of other assignments you’ve fallen behind on. Unfortunately the technology that makes AEDs function requires human intervention to ensure devices are ready to do their job.
AED technology has come a long way partly due to advances in battery life. AED units are typically guaranteed to operate four years or longer on a single non-rechargeable battery. Considering the energy required for an AED to operate for four years, this is a pretty impressive feat. Many devices will perform daily, weekly, or monthly self-tests which confirm that the circuitry, connections, pads, and batteries are all ready to function when deployed in an emergency.
Technological advancements have created a false sense of security when it comes to AED readiness. A 2011 study of AED failures identified that almost half of device failures were the result of pads or batteries – two items that require human intervention to ensure that they are functioning appropriately and not expired. Almost 8 years later, battery and AED technologies have improved well beyond the devices studied in 2011, there are thousands of additional devices deployed, and reliance only on the device “self-test” has increased.
Beyond the batteries and pads, there are several other important items that need to be regularly checked monthly to ensure that an AED is ready when needed:
Use of a professional external AED Liaison also provides peace of mind when it comes to AED response planning. An AED Liaison oversees AED response plans and protocols, training, deployment, maintenance, and reporting requirements when an AED is used. Some states mandate the use of an AED Liaison under law. In addition to monthly checks, the AED Liaison will make quarterly or annual site visits to ensure that the AED is functioning properly.
Ensuring all of the AEDs in your workplace are ready for emergency use is a huge responsibility that should never be taken lightly. Monthly checks help to identify when an AED has an expired part or needs a replacement item. Rotating the responsibility for the AED check (and still ensuring that it gets completed) helps to familiarize responders with AED locations, function, and contents.
Workforce safety managers should also follow the practice of “see something, say something” – look at public access AEDs in your schools, government buildings, and hotels. If you see something wrong, let the manager know so that they can address it. And let them know about this article!
Help Me Find a Course